Bitumen
Bitumen & Heavy Fuel
Bitumen or Asphalt is an oil-based substance with semi-solid hydrocarbon products produced by removing the lighter fractions from heavy crude oil during the refining process. As such, it is correctly known as refined bitumen. On the American side, bitumen is mostly known as Asphalt. While elsewhere, Asphalt or bitumen name is used for a mixture of small stones, sand, filler, and bitumen that is used for road paving material in the road construction industry. The asphalt or bitumen mixture contains approximately 5% bitumen. At ambient temperatures, bitumen is a stable and semi-solid substance. The vast majority of refined bitumen is used in construction. primarily as a constituent of products used in paving and roofing applications. As per requirements of the end-use bitumen is produced to specification either by refining process or blending. It is estimated that the current world use of bitumen is approximately 102 million tonne per year. Approximately 85% of all the bitumen produced is used as the binder in asphalt for roads in road construction.
Types of Bitumen and their Properties and Uses
- Penetration Grade Bitumen
- Oxidized Bitumen
- Cutback Bitumen
- Bitumen Emulsion
- Polymer – Modified Bitumen
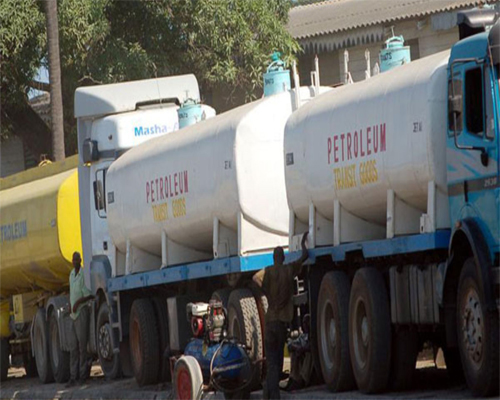
There are different types of bitumen available with different properties, specifications, and uses based on the requirements of the consuming industry. The specification of bitumen also shows the variation with safety, solubility, physical properties, and durability. To understand the performance of the bitumen when it is on service, the design of the physical properties of the material is highly essential. The standard testing methods are carried out to grade bitumen.
Our Best Solutions
Advanced Technology
Expert Engineers
Delivery On Time
The bitumen can be classified into the following grade types:
Penetration Grade Bitumen
The penetration grade bitumen is refinery bitumen that is manufactured at different viscosities. The penetration test is carried out to characterize the bitumen, based on the hardness. Thus, it has the name penetration bitumen. The penetration bitumen grades range from 15 to 450 for road bitumen. But the most commonly used range is 25 to 200. This is acquired by controlling the test carried out i.e. the distillation process. The partial control of fluxing the residual bitumen with the oils can help in bringing the required hardness.
The table below shows the penetration grade bitumen’s test carried out as per BS EN 12591. This test is for bitumen that is for road applications.
Table.1. Paving Grade Bitumen Specification As per BS EN 12591
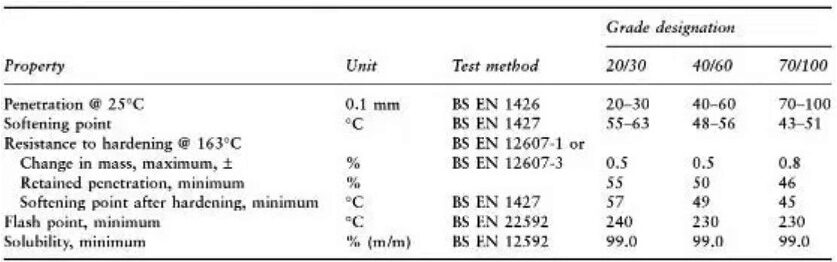
Cutback Bitumen Specification As per BS 3690: Part 1 & BS EN 12591Cutback Bitumen Specification As per BS 3690: Part 1 & BS EN 12591
The BS EN 1426 and BS EN 1427 provides the penetration and softening point values for the respective grades, as from Table-1. This will help in identifying the viscosity and the hardness of the bitumen grade.
The grades are represented by the penetration values i.e. For example, 40/60 as a penetration value of 50 ± 10.
The BS EN 13303 also gives the measure of loss on heating with respective limits for all penetration bitumen grades. This measure is to ensure that there are no volatile components present.
So, no component whose loss will contribute to the setting and hardening of bitumen during its preparation or lay course is undergone. The BS EN 12592 provides the solubility values to ensure that there is less or no impurities in the bitumen material.
Oxidized Bitumen
The refinery bitumen is further treated by the introduction of processed air. This will give us oxidized bitumen. By maintaining a controlled temperature, the air is introduced under pressure into soft bitumen.
Compounds of higher molecular weight are formed by the reaction of this introduced oxygen and bitumen components. Thus, the Asphaltenes and the Maltenes content increases resulting in a harder mix. This harder mix has a lower ductility and temperature susceptibility.
Oxidized Bitumen Oxidized Bitumen
The oxidized bitumen is used in industrial applications such as roofing and coating for pipes. By this method of processing, the bitumen that has a lower penetration can be manufactured, which can be employed for paving roads.
Cutback Bitumen
These are a grade of bitumen that comes under penetration grade bitumen. This type of bitumen has a temporarily reduced viscosity by the introduction of volatile oil. Once after the application, the volatile material is evaporated and bitumen gains its original viscosity.
The penetration grade bitumen is a thermoplastic material. It shows the different values of viscosity for different temperatures. In areas of road construction, it is necessary for the material to be fluid in nature at the time of laying i.e. during surface dressing.
It is also essential for the material to regain back to its original hardness and property after setting. This is ensured by cutback bitumen. The fluidity is obtained for any bitumen by raising the temperature. But when it is necessary to have fluidity at lower temperatures during surface dressing, cutback bitumen is employed.
The time for curing and the viscosity of cutback bitumen can be varied and controlled by the
dilution of volatile oil, and the volatility of the oil added.
70/100 or 160/220 pen bitumen that is diluted with kerosene is the main composition of bitumen in the construction of roads in the UK. The standard tar viscometer is used to test the standard viscosity.
The table-2 shows the cutback specifications based on BS 3690. This provides the requirement of the bitumen to satisfy solubility property, distillation property as well as recovery of properties after curing.
Table-2: The Cutback Bitumen Specification As per BS 3690: Part 1 & BS EN 12591
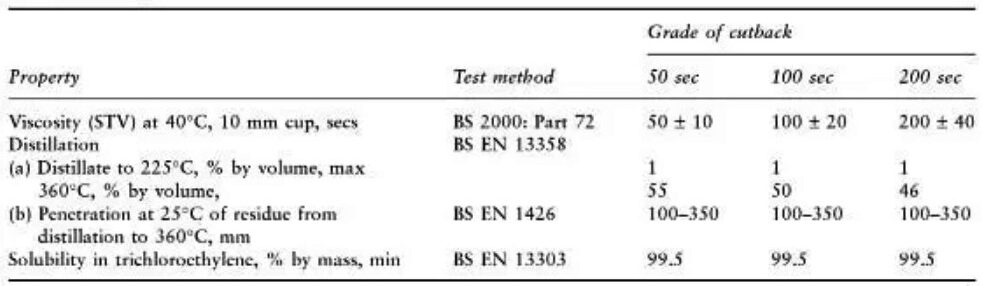
Cutback Bitumen Specification As per BS 3690: Part 1 & BS EN 12591Cutback Bitumen Specification As per BS 3690: Part 1 & BS EN 12591
Bitumen Emulsion
This type of bitumen forms a two-phase system with two immiscible liquids. One of them is dispersed as fine globules within the other liquid. When discrete globules of bitumen are dispersed in a continuous form of water, bitumen emulsion is formed.
This is a form of penetration grade bitumen that is mixed and used for laying purposes.
An emulsifier having a long hydrocarbon chain with either a cationic or anionic ending is used for dispersing the bitumen globules. This emulsifier provides an electrochemical environment. The ionic part of the chain has an affinity towards the water and the bitumen is attracted by the hydrocarbon part.
Types Bitumen Emulsion
As shown in the figure below, the hydrocarbon binds the bitumen globules strongly and the ionic part is seen on the surface of the globules. Depending on the ions present, the droplets take a charge.
The emulsions can be cationic (positive charge) or anionic (negatively charged). The globules of the same charge hence repel each other, making the whole system stable. To facilitate adhesion with the aggregates (that are negatively charged), cationic emulsions are more preferred.
Bitumen during Dispersion in an emulsifier
- Types of bitumen emulsifier and its quantity
- Water evaporation rate
- Bitumen quantity
- Bitumen globules size
- Mechanical forces
The emulsions are applied by using sprays. For this viscosity is a primary concern. With the increase of bitumen content, the mixture becomes more viscous. This is found to be sensitive when the amount exceeds 60%.
The BS 434: Part 1 and BS EN 13808 gives the specification for the viscosity of road emulsions.
Polymer – Modified Bitumen
Polymer modified bitumen is the type of bitumen obtained by the modification of the strength and the rheological properties of the penetration graded bitumen. Here for this 2 to 8% of polymer is added.
Polymer – Modified Bitumen Polymer – Modified Bitumen
The polymer used can be either plastic or rubber. These polymers vary the strength and the viscoelastic properties of the bitumen. This is achieved by:
- Elastic response increase
- Improvement in cohesive property
- Improvement in Fracture strength
- Providing ductility
Some of the examples of rubber polymers used are styrene block copolymers, synthetic rubbers, natural and recycled rubbers. Plastics that are thermoplastic polymers are also used.